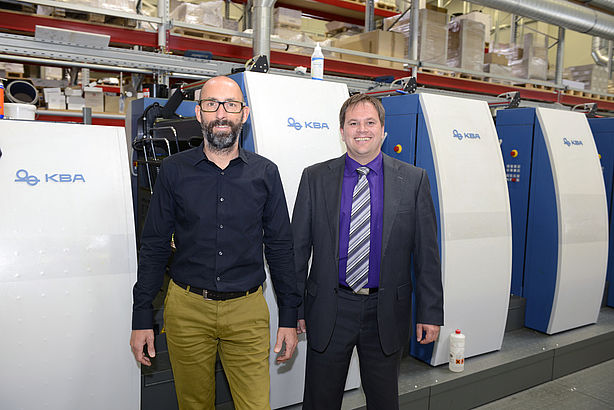
Up until now production on uncoated stock took place on a Rapida 105 universal with highly pigmented Aniva ink. A prerequisite for this is the high gamut workflow which was developed in-house and significantly extends the colour space compared to the PSO standard (ISO 12647). Additionally, years of experience and extensive tests allowed the company to develop ICC profiles which are suited to varying degrees of substrate absorption. When printing on uncoated stock Vogl is thus able to produce results that are identical to those of coated paper in terms of their image definition, colour scheme and saturation. Or the other way around, the final results a customer expects on illustration printing paper should also be what he gets on uncoated stock.
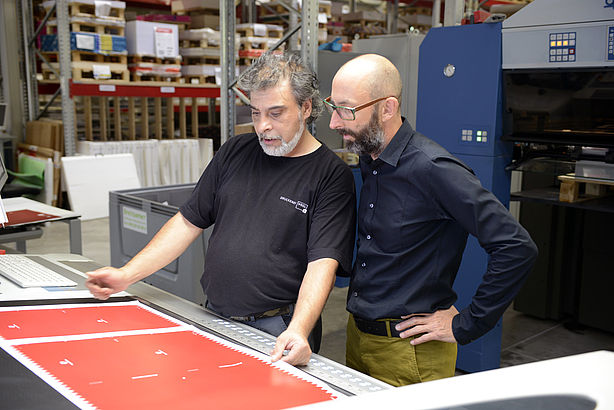
Rich colours and calm surfaces
Impressive print samples with calm surfaces and luscious colours today are proof. In order to make his customers change their way of thinking, Ralf Vogl takes their old job data and prints onto uncoated stock letting them compare. They then see what is possible from a technological point of view today and how different the results are compared to printing in the past, especially as “each of them have had bad experiences with uncoated stock”, the managing director knows. Today Vogl is the only printing company in and around Munich which specialises in printing on this special stock. He believes he is some two to three years ahead of this market segment, nevertheless he knows that others can easily catch-up with new technology.
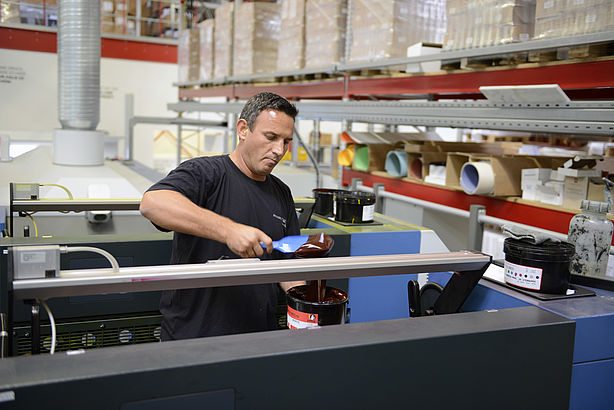

More jobs per shift
Two reasons in particular tipped the scales in favour of the high-performance Rapida: its high level of automation with minimal makeready times and its outstanding print results in UV printing. Makeready times are a priority given the firm’s average job size of between 2,000 and 3,000 sheets and a raft of single jobs with one to four formes. Its high speed of up to 18,000sph is ultimately of secondary importance. However, a large speedometer displays how fast the press is running in the press room, pre-press and meeting rooms. “This motivates our press operators and impresses our visitors,” says Ralf Vogl. Customers often come from other cities to accept printwork, sometimes also from Paris.
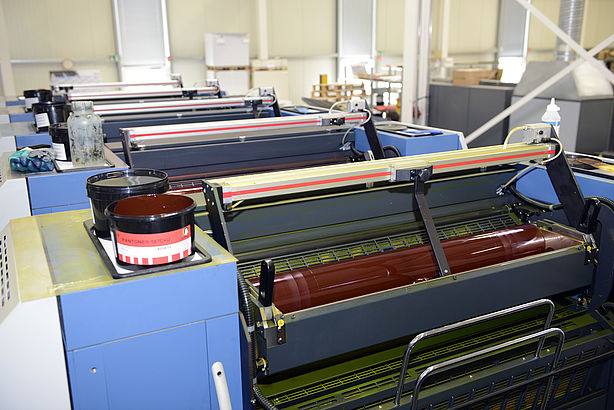
The company is flexible when it comes to UV curing. Depending on job, the dryers can be placed between the delivery extension and the individual printing units, they can be moved to where they are needed. Furthermore, an advantage of UV printing is that powder is no longer necessary. This results in longer cycles in between washing the blanket as well as less cleaning and maintenance. Powder does not collect in the first unit any more when perfecting in the second pass.
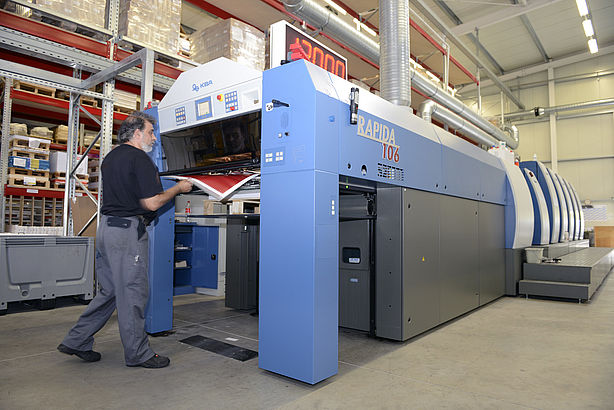
Lenticular printing as a further business field
The Rapida 106 is also equipped for film printing as Vogl aims to serve the film market in the future and print lenticular films. This was kept to small format in the past due to the platesetters. This business field is expected to be expanded into medium format with the purchase of new platesetters. It is as challenging as printing on uncoated stock, but more profitable than the production of standard print products.
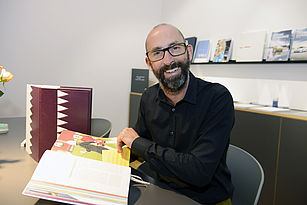
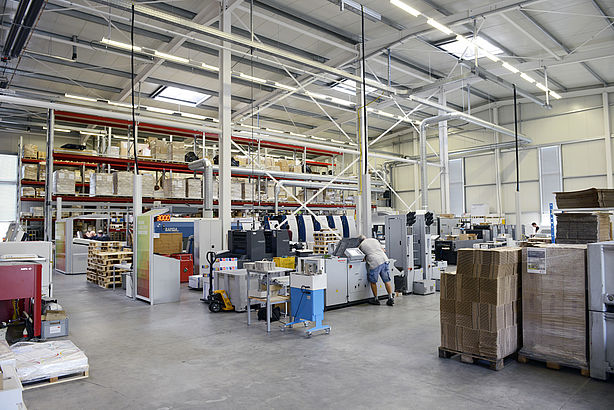
Ralf Vogl passes those highly specialised processes which cannot be carried out on-site on to reliable partner businesses. In this way the customer, predominantly agencies, receive the total package from one source.
The new, cutting-edge headquarters in Zorneding is not the company’s first site. Founded in 1956, it has moved many times in Munich and has been continually expanded. It has 25 employees and operates in three shifts.