Plate detection before the change process
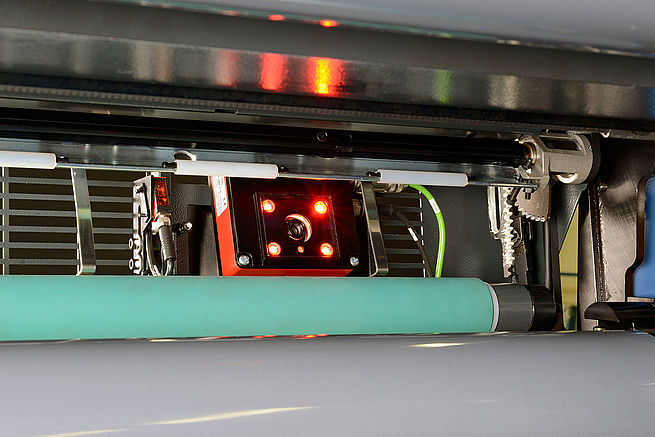
DriveTronic Plate Ident was to date only available for presses of the Rapida 106, Rapida 145, Rapida 164 and MetalStar 3 series with DriveTronic SPC. With immediate effect, however, it is now offered as an option for all presses with FAPC plate changers. That means that the half-format presses Rapida 75 PRO and Rapida 76 can also be configured with this additional automation function for FAPC in future.
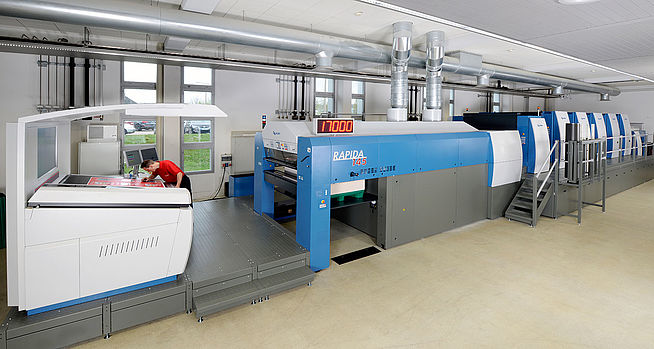
Automatic correction of the plate position
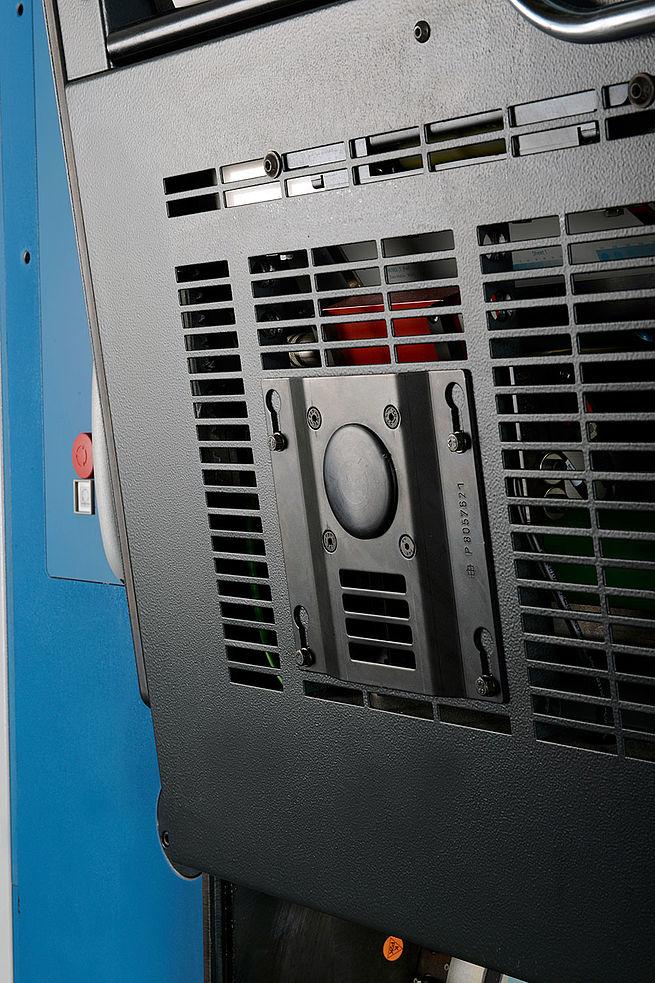
Plate Position Check is an additional function of DriveTronic Plate Ident to permit automatic correction of the plate position already before the first sheet is printed. It evaluates the relative positions of the plates and corrects the plate cylinders accordingly. In most cases, only minimal register corrections remain to be made after checking of a first sample sheet before full job production begins. Users who wish to move straight on to production without stopping to check a sample sheet are recommended to consider the inline QualiTronic ICR system.
Plate Position Check is aimed above all at print companies where plates are still punched manually. The punching accuracy of modern CtP systems is generally such that the Plate Position Check function is superfluous, provided all the plates for a given job were punched on the same device.
The right plates in the right place
While the job presetting data such as ink profiles, duct roller speeds and area coverage are being transferred to the Rapida press from the PPS system LogoTronic Professional or via CIPLinkX, DataMatrix Select checks that the new plates to be mounted actually belong to the current job or section of a job, and furthermore that the colour sequence matches the press configuration. In this way, DataMatrix Select is a further significant step towards full process management.
Any incorrect plate assignments are immediately detected and signalled to the operator. In addition, the possibilities for cost accounting after completion of a job are improved.
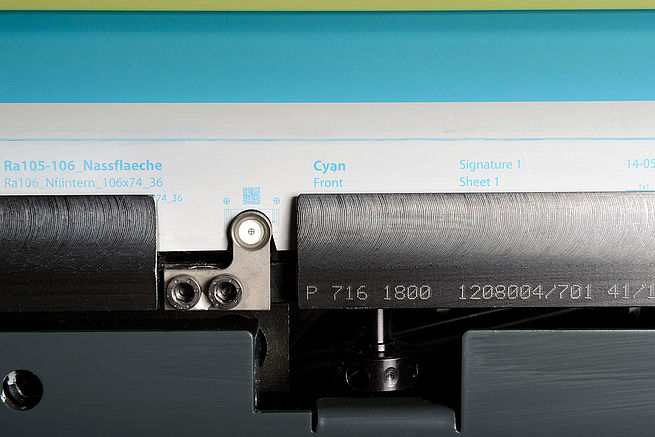
Two data matrix codes are exposed onto each plate together with the register marks used by DriveTronic Plate Ident (see photo 1). After reading the codes from each printing unit, LogoTronic Professional or CIPLink X compares the data with those held in a central database. On the basis of the code data, various plausibility checks are performed, e.g. correct plates for the current job, plates mounted on the correct printing units, plates with correct colour separations, or correct language versions. In this respect, the data matrix code permits unambiguous identification of every printing plate.
The combination of fully automatic plate changing and the additional functions offered by the plate detection system DriveTronic Plate Ident achieves a significant increase in productivity for printers faced with ever shorter run lengths and thus frequent job changeovers. The reduction in start-up waste improves profitability, and errors in connection with plate changes become a thing of the past.