- Used for in-mould label production
- Pioneer on the Polish market
- Production output practically doubled
Top-Pol in Zbrosławice is the first print company in Poland to use a Rapida RDC 106 rotary die-cutter from Koenig & Bauer. The machine was purchased as part of a project to allow the printing of innovative IML labels in an offset process, and which received funding support from the EU. The rotary die-cutter aims to guarantee production stability and high cutting speeds, alongside significantly reduced makeready times.
Top-Pol is a family-run company that has been active on the printing market since 1989, and has become a specialist for the production of labels using non-absorbent substrates – primarily plastics – since the end of the 1990s. Co-proprietor Marcel Topolski: “We were one of the pioneers in the use of UV offset technologies for substrates like this. IML labels soon became our flagship product and currently account for 70 to 80 per cent of our production volume. Another key area is the production of lids and covers made from PE, PS or PP for plastic packaging, for example for yoghurt pots.”
Top-Pol exports 30 to 40 per cent of its production output. The end customers for the labels are primarily companies operating in the food and construction industries. “The systematic development we are pursuing means we are constantly modernising our production machinery, also with regard to finishing processes,” says Marcel Topolski.
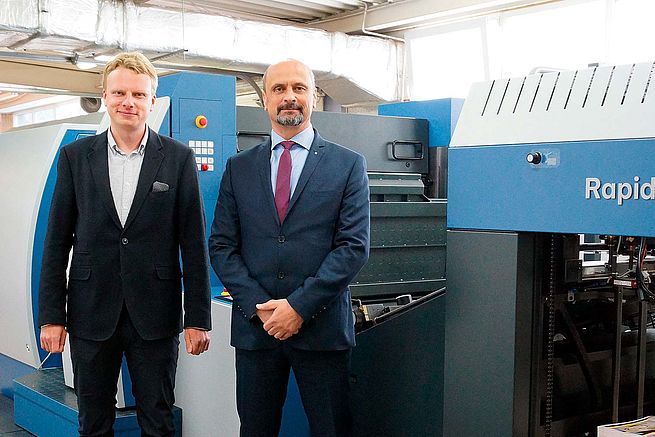
High production speeds, fast makeready
The maximum mechanical output of the Rapida RDC 106 totals 15,000 sheets per hour. The press enables the die-cutting of substrates in thicknesses from 0.03 to 0.6 mm, and is equipped with numerous solutions that were introduced with the Rapida 106 sheetfed offset printing presses. These include, among others, DriveTronic technology with dedicated drives, the sidelay-free infeed DriveTronic SIS, and a camera system to monitor sheet travel at the feeder and delivery.
One of the key functions of the machine is automatic adjustment of the die-cutting pressure. The pressure can be set separately for each side of the cylinder with a precision of 1 µm. This results in a high die-cutting quality over the entire length of a run. Fast, tool-free forme changes that use a “click & cut” process enable very short makeready times – as little as 5 minutes for repeat jobs. Smooth delivery of the sheets onto the pallet is realised by the dynamic sheet brake and an anti-static system with an extensive range of functions. This also allows further processing to continue immediately when the next step in the production chain starts. There is no need for time-consuming re-stacking ahead of automated further processing. The die-cutting units are equipped with a magnetic cylinder, to which the individual cutting formes are fixed. As a result, a range of processes can be realised in a single unit – from die-cutting to embossing or perforation, along with hole punching. The Rapida RDC 106 is available in a number of different configurations with one to four units.
Enhanced production and productivity
“Once again, we have assumed a pioneering role, this time by introducing the Rapida RDC 106 onto the Polish market,” says Marcel Topolski. “As we had already been successful using rotary label die-cutting in the past, the purchase was an ideal opportunity to continue to enhance our productivity and production. After all, our products are quite difficult to produce. The IML labels are made of plastic and also feature indentations to make it easier for the end customer to separate them later on. This makes it a perfect opportunity to broaden our knowledge, both for our own and for the manufacturer's benefit.”
“Special mention must be made of the level of dedication shown not only by the sales team but also by the technical and service departments, both at our local Koenig & Bauer branch office and at the German headquarters. Integration of the press into the new technological process was completed efficiently and on-time during the first quarter of the year. Our operators have nothing but praise for it, especially in regard to the increased level of process stability and the doubling of production output compared to our previous solution.”
“Our customers in the food industry, along with our customers in other sectors, expect labels of the highest quality. Accordingly, the solutions we use must also represent the highest standards and the best possible performance that the global market has to offer. The latest investment in the Rapida RDC 106 will more than satisfy these expectations, which are becoming more and more demanding due to changes to the market and to consumer tastes. These aspects are all the more important in the current global situation, which has, of course, also impacted our order volume,” Marcel Topolski concludes.
Jan Korenc, managing director of Koenig & Bauer (CEE) adds: “This is a first-class solution which requires up to 40 per cent less makeready to complete an entire job. This is why we are confident that it will contribute to the continued growth of Top-Pol as one of the leading print companies in Poland, and play a role in the successful implementation of the new technology project for which the Rapida RDC 106 rotary die-cutter was purchased.”