- New plate changer enhances productivity
- Saved time can be used for additional print jobs
- QualiTronic SheetDetect for automatic makeready
- Waste reduced to an absolute minimum
FLYERALARM is one of the largest online printer in Germany and currently posts an annual turnover of some €330 million. Even at European level, the family-run company must be counted among the leaders with its 2,000 employees. At just the eight production plants in Northern Bavaria and in Saxony, FLYERALARM Industrial Print operates 90 printing units, predominantly in large format and among them also several Rapida 145 presses.
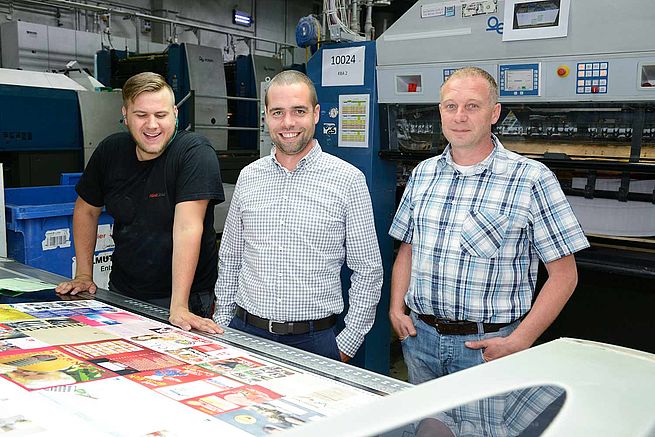
The assignment of print jobs to individual plants and presses is decided on the basis of substrate, grammage and product type. The plant in Greussenheim near Würzburg, for example, is specialised on conventional print products on glossy substrates. Two different grammages are printed, namely 135 and 250 g/m2, and the three four-colour Rapida 145 presses produce mainly flyers, folders and magazines. The average run length lies below 5,000 copies, and it is only rarely that orders come in for as many as 30,000 copies. With so many short runs, fast job changes are naturally all the more important.
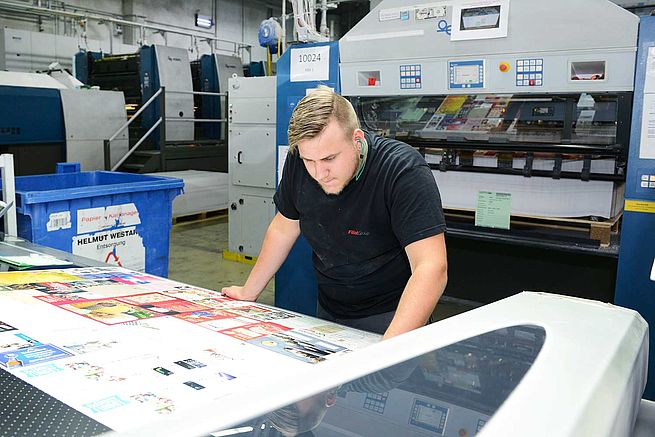
The Rapida 145 large-format presses at the plant in Greussenheim are equipped with a full spectrum of automation modules geared to fast job changes. This includes DriveTronic components such as SIS (sidelay-free infeed) and SPC (simultaneous plate change), CleanTronic Synchro washing systems, a special ink duct coating for fast ink changes, online integration with the LogoTronic Professional management system, and many others besides. Accordingly, fast job changes with automatic plate changing, parallel washing and delivery of the first test print from a new job within five minutes were already standard. Through the incorporation of optimised plate changers and adaptation of the washing programs to the correspondingly shorter change time, however, makeready times in Greussenheim have now been reduced further still. In the meantime, a complete changeover from the last good sheet of one job to the first good sheet of the next takes only half the previous time, as plant manager Johannes Barthelmes confirms.
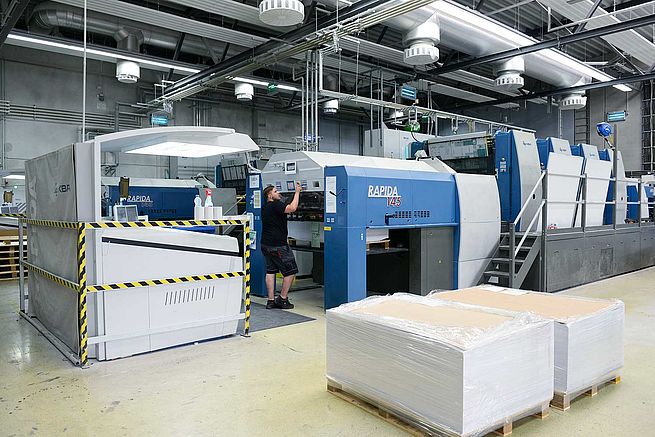
QualiTronic SheetDetect supports automated printing
FLYERALARM combines the efficiency of simultaneous plate changing with the enormous additional potential of PlateIdent. As soon as the data matrix codes on the plates are read, all the necessary press presetting information is loaded directly from LogoTronic Professional. Johannes Barthelmes: “For us, that is a form of semi-automated printing. While the press is in makeready, the printers and helpers have time to attend to other tasks.”
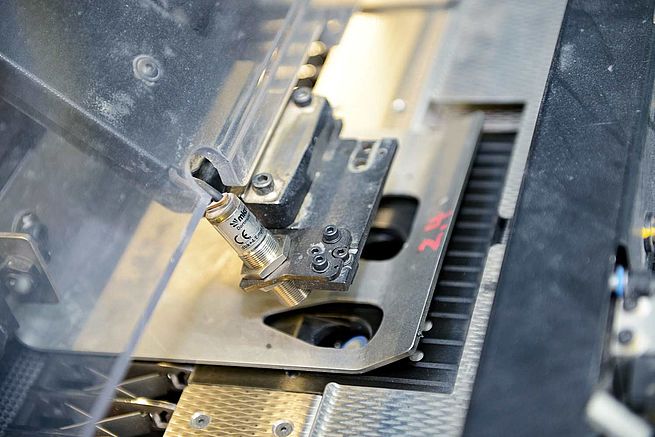
Normally, several print jobs are stacked together on a single pallet. At the end of each job, the pile is marked with a fluorescent pen, taking into account a defined production allowance and any waste sheets. After turning, QualiTronic SheetDetect recognises the marked sheets by way of a sensor under the infeed, enabling separation of the individual jobs. The Rapida 145 detects the end of a job and starts makeready for the subsequent job in the same manner as ErgoTronic AutoRun. For the helpers on the presses, this means less time to be spent at the feeder and more time for the loading of new plates into the plate changers.
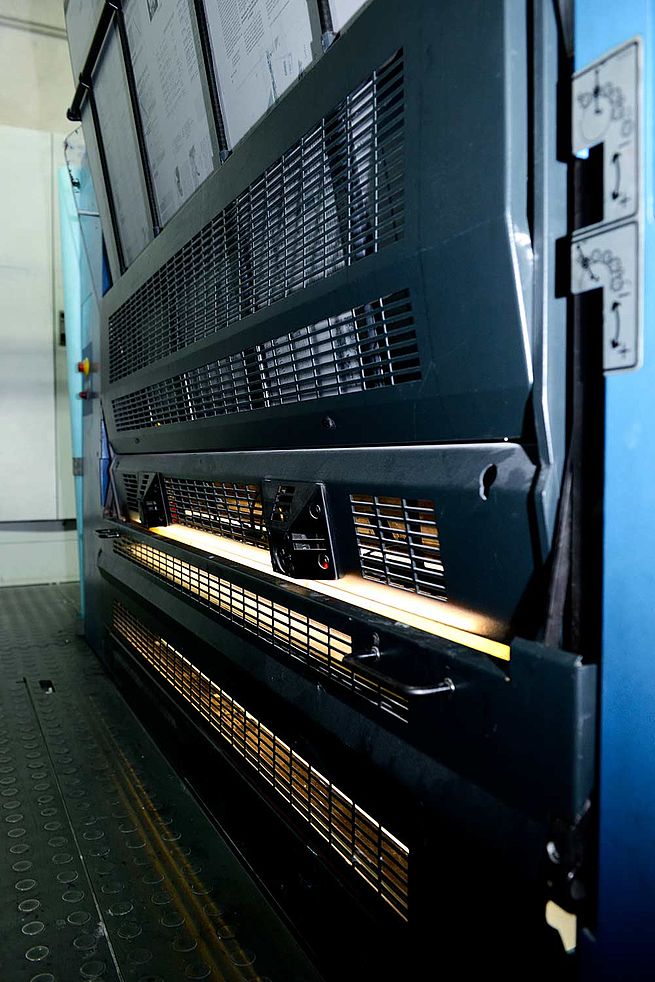
Inline quality reduces waste
The three Rapida 145 presses are equipped with QualiTronic ColorControl for inline colour measurement. On this basis, waste has been cut by around 50 per cent compared to the previous Rapida 142 presses. Automatic positioning of the plates with PlateIdent also contributes to waste reduction.
There are many aspects of the Rapida technology which Johannes Barthelmes and his colleagues mention as especially advantageous for the business model pursued by FLYERALARM – from the outstanding stability and reliability, to unrivalled speed in production and not least the exceptionally fast makeready. In addition, a close technology partnership drives developments which also benefit other print companies. One example is the new plate changer, which is now officially available to the market.
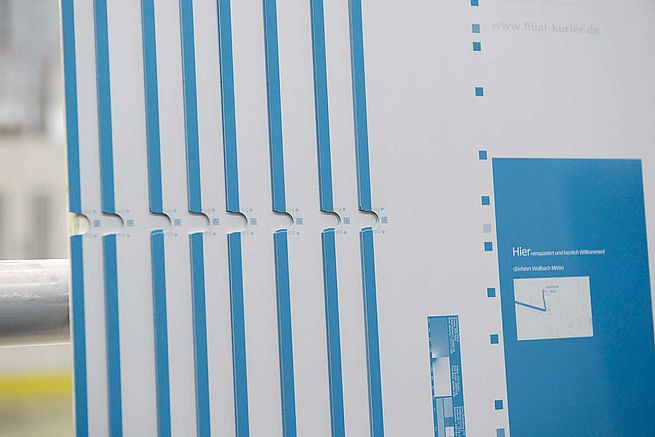
Primarily in-house value chain
Day after day, approx. 350,000 printed sheets leave the FLYERALARM plant in Greussenheim. The portfolio of the company group embraces a total of almost 3 million different products and product variants. Unlike other providers, FLYERALARM itself handles the entire value chain for its principal products in the fields of print and advertising. The 2,000 employees print, finish and dispatch some 15,000 jobs every day.